As we all know, having the proper amount of oil mixed in the gas of our carbureted 2-stroke outboards is critical. Automatic, variable oil injection makes our lives much simpler (and cleaner), but if the oil injection system on your outboard fails the result is catastrophic.
All carbureted Mercury 2-strokes that I?m familiar with employ an oil pump that is driven by a bevel gear on the crankshaft. At first glance this is a very simple and reliable way to provide oil injection, but it is not without potential problems. On some engines Mercury used a plastic gear to drive the oil pump, and these have been known to fail.
On larger Mercury models there is a rotation sensor on the oil pump. If the pump stops rotating (and thereby stops pumping oil) an alarm sounds. This is pretty good protection, but alas my 1998 115 2+2 does not have a rotation sensor. That means that I have no warning system of any kind to tell me if my oil pump fails. But even if a rotation sensor is present, there are still ways that you can loose oil injection and not know it until your engine seizes. Broken or split hoses and failed hose clamps are some possibilities.
Marine Solutions (www.marinesolutionswi.com) has developed a product called the ?Oil Watch Monitor? which solves all the above mentioned problems. The Oil Watch Monitor is spliced into the oil feed line and monitors the pulses of oil pressure. If the pulses stop, an alarm sounds. The Oil Watch Monitor also acts as a redundant alarm in the event that you run out of oil, although you would not want to rely on the Oil Watch Monitor for that purpose, since it would not sound until you were completely out of oil and running without any lubrication.
Here are some pictures of how I installed an Oil Watch Monitor on my 1998 115:
This picture shows the Oil Watch monitor before I installed it.
(Deleted because Iboats only allows 6 pictures...)
Here is the oil feed line going from the oil pump on the right to the check valve on the left
First I cut the oil feed line and installed a Tee fitting
It?s important to bleed all the air out of the oil lines so that the Oil Watch Monitor can accurately sense pressure pulses. In this picture I have plumbed the Oil Watch Monitor, but I have it rotation upside down on the Tee fitting. I then stuck a nylon 90 degree elbow on the exit side as shown
To purge the lines of air I started the outboard on a 50:1 premix and ran it until oil was pumped out of the line. Actually, my intent was to run the engine until oil pumped out of the line, but the 90 degree elbow was translucent enough that I could easily see when it started to fill with oil and I cut the engine before any oil pumped out. I was surprised at how slowly the oil moved through the line.
After I purged the oil out of the lines I replaced the 90 degree elbow with a plug. The plug looks like a hack job from this picture, but it?s a little more polished than it appears.
Finally I rotated the Oil Watch Monitor about the Tee fitting to it?s proper position and applied a hose clamp.
Here is a view from the top
The only remaining step was to make the electrical connections so that my existing warning horn would sound if oil pulses are not present.
In actual use the warning horn sounds when I turn on the ignition, and goes out when the engine starts (actually, it usually goes out while cranking). I?ve tested the function of the Oil Watch Monitor by using the lanyard kill switch to stop the engine while the ignition is still on, and as soon as the engine stops the alarm horn sounds.
All carbureted Mercury 2-strokes that I?m familiar with employ an oil pump that is driven by a bevel gear on the crankshaft. At first glance this is a very simple and reliable way to provide oil injection, but it is not without potential problems. On some engines Mercury used a plastic gear to drive the oil pump, and these have been known to fail.
On larger Mercury models there is a rotation sensor on the oil pump. If the pump stops rotating (and thereby stops pumping oil) an alarm sounds. This is pretty good protection, but alas my 1998 115 2+2 does not have a rotation sensor. That means that I have no warning system of any kind to tell me if my oil pump fails. But even if a rotation sensor is present, there are still ways that you can loose oil injection and not know it until your engine seizes. Broken or split hoses and failed hose clamps are some possibilities.
Marine Solutions (www.marinesolutionswi.com) has developed a product called the ?Oil Watch Monitor? which solves all the above mentioned problems. The Oil Watch Monitor is spliced into the oil feed line and monitors the pulses of oil pressure. If the pulses stop, an alarm sounds. The Oil Watch Monitor also acts as a redundant alarm in the event that you run out of oil, although you would not want to rely on the Oil Watch Monitor for that purpose, since it would not sound until you were completely out of oil and running without any lubrication.
Here are some pictures of how I installed an Oil Watch Monitor on my 1998 115:
This picture shows the Oil Watch monitor before I installed it.
(Deleted because Iboats only allows 6 pictures...)
Here is the oil feed line going from the oil pump on the right to the check valve on the left
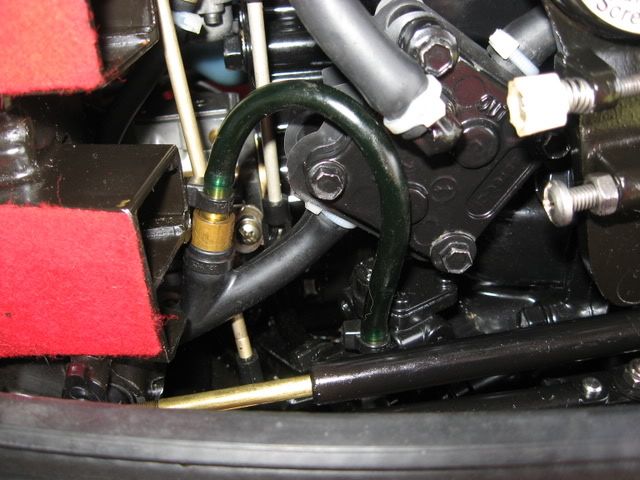
First I cut the oil feed line and installed a Tee fitting

It?s important to bleed all the air out of the oil lines so that the Oil Watch Monitor can accurately sense pressure pulses. In this picture I have plumbed the Oil Watch Monitor, but I have it rotation upside down on the Tee fitting. I then stuck a nylon 90 degree elbow on the exit side as shown
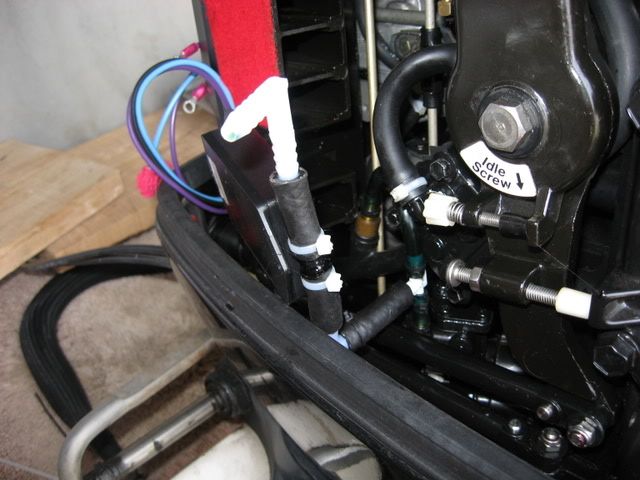
To purge the lines of air I started the outboard on a 50:1 premix and ran it until oil was pumped out of the line. Actually, my intent was to run the engine until oil pumped out of the line, but the 90 degree elbow was translucent enough that I could easily see when it started to fill with oil and I cut the engine before any oil pumped out. I was surprised at how slowly the oil moved through the line.
After I purged the oil out of the lines I replaced the 90 degree elbow with a plug. The plug looks like a hack job from this picture, but it?s a little more polished than it appears.
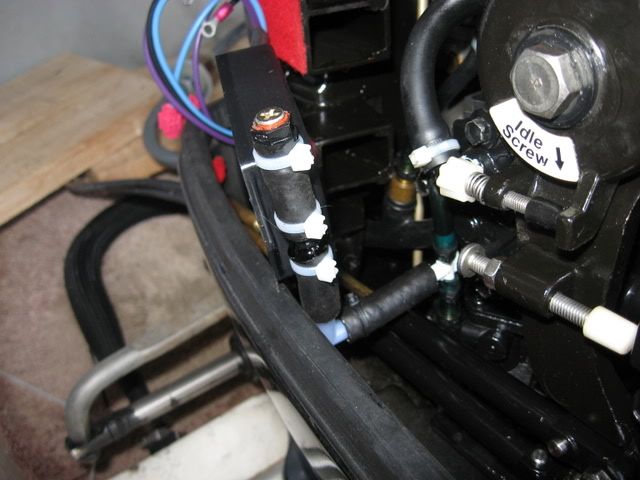
Finally I rotated the Oil Watch Monitor about the Tee fitting to it?s proper position and applied a hose clamp.
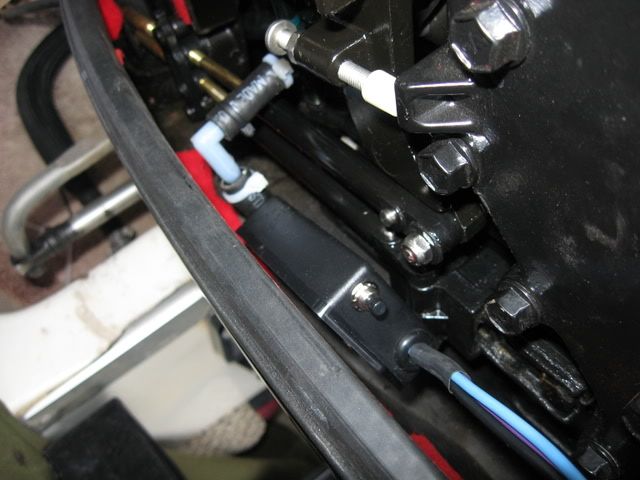
Here is a view from the top
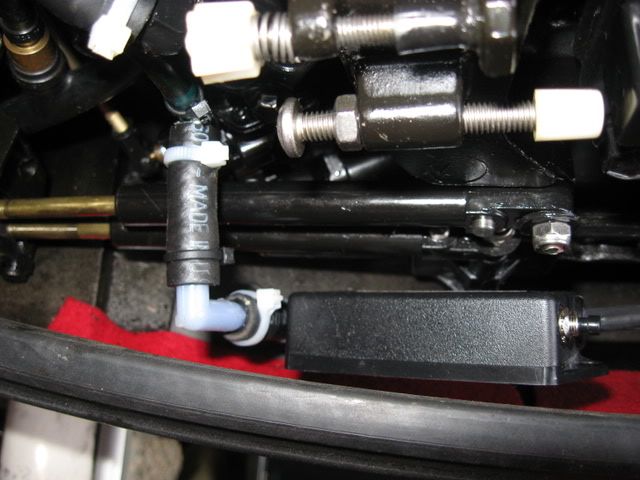
The only remaining step was to make the electrical connections so that my existing warning horn would sound if oil pulses are not present.
In actual use the warning horn sounds when I turn on the ignition, and goes out when the engine starts (actually, it usually goes out while cranking). I?ve tested the function of the Oil Watch Monitor by using the lanyard kill switch to stop the engine while the ignition is still on, and as soon as the engine stops the alarm horn sounds.