MarcelSydney
Seaman
- Joined
- Jul 5, 2021
- Messages
- 56
Alpha one gen 2.
I have spent the past day trying to get a gimble bearing out and it is not budging. At all, not a bit.
There was water in the bellows when I pulled of to inspect so it looks corroded. (I will probably be doing the bellows and the uni joints too as a result by the look of them).
I snapped a wrench with the force (had a lever on it) and wrecked the brand new bearing puller as well as the thread has seized, presumably cold welded. Fortunately when I let the pressure go from the internal thing a me jig in the jaws, it it literally popped out of the bearing, so I avoided the trouble of cutting the tool out. Small win.
I have been searching everywhere, but not a lot on the topic other than persisting, go harder etc but these bearing pullers aren't cheap here in Oz and i imagine the same thing will happen again. I will have to buy another one, but before wrecking the next one, it would be good to get the bearing to loosen a touch somehow.
I read on some old forums to drill 2 holes in the outer race (i think in red where marked on attached), and then hit it with a cold chisel to try and split it. I'm concerned about possible collateral damage. I'm not sure how close to the edge of the bearing to drill or what's behind it in case I go to deep.
Does this work?
Any other ideas?
Thanks
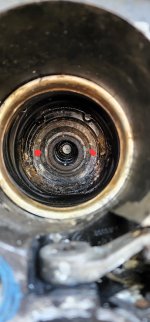
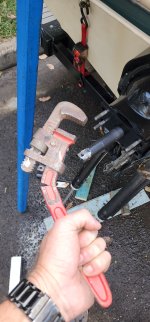
I have spent the past day trying to get a gimble bearing out and it is not budging. At all, not a bit.
There was water in the bellows when I pulled of to inspect so it looks corroded. (I will probably be doing the bellows and the uni joints too as a result by the look of them).
I snapped a wrench with the force (had a lever on it) and wrecked the brand new bearing puller as well as the thread has seized, presumably cold welded. Fortunately when I let the pressure go from the internal thing a me jig in the jaws, it it literally popped out of the bearing, so I avoided the trouble of cutting the tool out. Small win.
I have been searching everywhere, but not a lot on the topic other than persisting, go harder etc but these bearing pullers aren't cheap here in Oz and i imagine the same thing will happen again. I will have to buy another one, but before wrecking the next one, it would be good to get the bearing to loosen a touch somehow.
I read on some old forums to drill 2 holes in the outer race (i think in red where marked on attached), and then hit it with a cold chisel to try and split it. I'm concerned about possible collateral damage. I'm not sure how close to the edge of the bearing to drill or what's behind it in case I go to deep.
Does this work?
Any other ideas?
Thanks
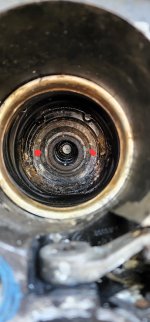
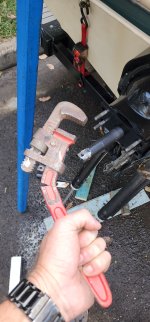