Last fall I purchased a 1990 90-hp Force that hadn't been run in almost 2 years and I have spent this season getting it up and running. After finally getting the mechanical issues sorted out, I decided to redo the foam insulation in the cowling/outboard cover in order to quiet her down. There was pretty much no insulation left when I purchased it, except for some small patches attached to old glue, which made her very noisy. I did some research on the hull truth and decided to fix this myself.
Here is my cowling
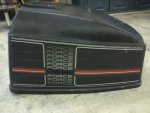
Next I used isopropyl alcohol and a razor/scrapper to clean out the remaining foam, glue, and residue. It actually took me a good hour or two to fully clean it out and this was the end result.
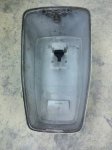
Next I gathered my materials including 3M-90 aerosol spray glue and silver tape.
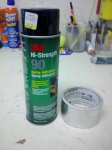
....and I couldn't forget about the foam! I used a product from Sound Down that was 1/2-inch thick and had a mylar face to protect the foam from gas and heat. Sound Down has two layers of foam sandwiched together that is separated by a vinyl barrier. This product is pricey and cost me about $70 for a 32inx54in piece.
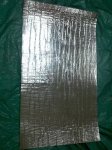
Next I started to create stenzels inside the cowling out of paper. Then I careful cut each section piece by piece, and then fit it into place and trimming where necessary before moving onto the next piece. Once the piece fit I sprayed both the cowling and foam contact surfaces with the 3M-90 and pressed them into place. I did have to make some shim pieces out of scrap to fill small gaps.
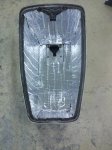
Lastly, once all the pieces were glued into place I covered up all the edges with silver tape to keep water/gas from getting into the foam and keep the edges in place.
https://lh5.googleusercontent.com/-...epaU/w865-h646-no/2013-07-21_13-14-02_889.jpg
I tested the new insulation out this morning on the water and it did make a big a difference. Note that this foam is pretty heavy and added significant weight to the cowling....it may have actually doubled in weight!
Here is my cowling
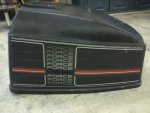
Next I used isopropyl alcohol and a razor/scrapper to clean out the remaining foam, glue, and residue. It actually took me a good hour or two to fully clean it out and this was the end result.
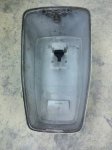
Next I gathered my materials including 3M-90 aerosol spray glue and silver tape.
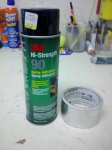
....and I couldn't forget about the foam! I used a product from Sound Down that was 1/2-inch thick and had a mylar face to protect the foam from gas and heat. Sound Down has two layers of foam sandwiched together that is separated by a vinyl barrier. This product is pricey and cost me about $70 for a 32inx54in piece.
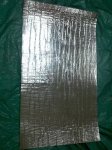
Next I started to create stenzels inside the cowling out of paper. Then I careful cut each section piece by piece, and then fit it into place and trimming where necessary before moving onto the next piece. Once the piece fit I sprayed both the cowling and foam contact surfaces with the 3M-90 and pressed them into place. I did have to make some shim pieces out of scrap to fill small gaps.
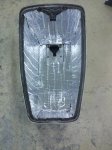
Lastly, once all the pieces were glued into place I covered up all the edges with silver tape to keep water/gas from getting into the foam and keep the edges in place.
https://lh5.googleusercontent.com/-...epaU/w865-h646-no/2013-07-21_13-14-02_889.jpg
I tested the new insulation out this morning on the water and it did make a big a difference. Note that this foam is pretty heavy and added significant weight to the cowling....it may have actually doubled in weight!
Last edited: