Boomyal
Supreme Mariner
- Joined
- Aug 16, 2003
- Messages
- 12,072
I thought that this would be of general interest. I am imbarking on my second fiberglass part making project. Ya'll might remember my first ever project which was a water deflecter shield for the gas tank bay of my Gulfstream.
My current project is a drink holder for the front of the engine cover on my new BeachCraft. It is actually a coverup for a mistake I made in trying to cut down what I considered the excessive length of the doghouse.(more on that later) I was wanting to get more floor space in this boat as it is 2 ft shorter than my Gulfstream. Both boats have the same engine so the motor used up more of the cockpit area in the shorter BeachCraft. Additionally, I felt that they made the bilge and motor cover to accomodate a six cylinder as well as the shorter V8.
So I undertook to cut off the rear of the doghouse to move the engine cover back, giving me six more inches of floorspace. I will have to scab in a piece of plywood to cover the now exposed opening in the bilge, forward of the front of the cut down doghouse. Good idea but I goofed and cut off too much. So I had to cut a hole in the front of the doghouse so the waterpump pulley would clear it. Now I am attempting to build a clever part to cover the mistake. I'll show pictures of the doghouse later.
For right now I wanted to chronicle the manufacture process of the part.
I started by making a male plug for the part: I would spray on a mold release and build the part, a layer at a time, over the top of the plug.
I started to lay up the glass cloth (picture has two layers) but was finding that the shape was making it difficult to wrap the glass and keep it well adhered to the previous application. You can also see on the forward wall where I had pieced remnants in to keep the thickness constant.
In my internet boating career I remembered seeing information about vacuum bagging and figured that would be the answer to my problem. Question was how to accomplish that without any experience and without costing an arm and a leg. I vowed that this Beachcraft project was going to be an economy project.
I now have the answer to those issues. I have obtained 66 sq yds of very slightly irregular 10oz Eglass off of ebay for about 2 bucks a yard shipped (you cannot use the dollar sign in this forum. It shows up as you type it but does not show once you post) US Composite sell the same glass for 6.70 a yard.
I also scavanged two different vacuum pumps. (an extra just in case) I have the plastic wrap material (old roll of plastic sheet from the garage) and this weekend I will attempt the process. The large board you see my part sitting on is the first step. Note the little bud coming up thru the board at the front end of the glassed part. That is my vacuum port. (a metal tire valve with rubber washers) I will post pictures as I set the rest of the process up and begin the bagging.

My current project is a drink holder for the front of the engine cover on my new BeachCraft. It is actually a coverup for a mistake I made in trying to cut down what I considered the excessive length of the doghouse.(more on that later) I was wanting to get more floor space in this boat as it is 2 ft shorter than my Gulfstream. Both boats have the same engine so the motor used up more of the cockpit area in the shorter BeachCraft. Additionally, I felt that they made the bilge and motor cover to accomodate a six cylinder as well as the shorter V8.
So I undertook to cut off the rear of the doghouse to move the engine cover back, giving me six more inches of floorspace. I will have to scab in a piece of plywood to cover the now exposed opening in the bilge, forward of the front of the cut down doghouse. Good idea but I goofed and cut off too much. So I had to cut a hole in the front of the doghouse so the waterpump pulley would clear it. Now I am attempting to build a clever part to cover the mistake. I'll show pictures of the doghouse later.
For right now I wanted to chronicle the manufacture process of the part.
I started by making a male plug for the part: I would spray on a mold release and build the part, a layer at a time, over the top of the plug.
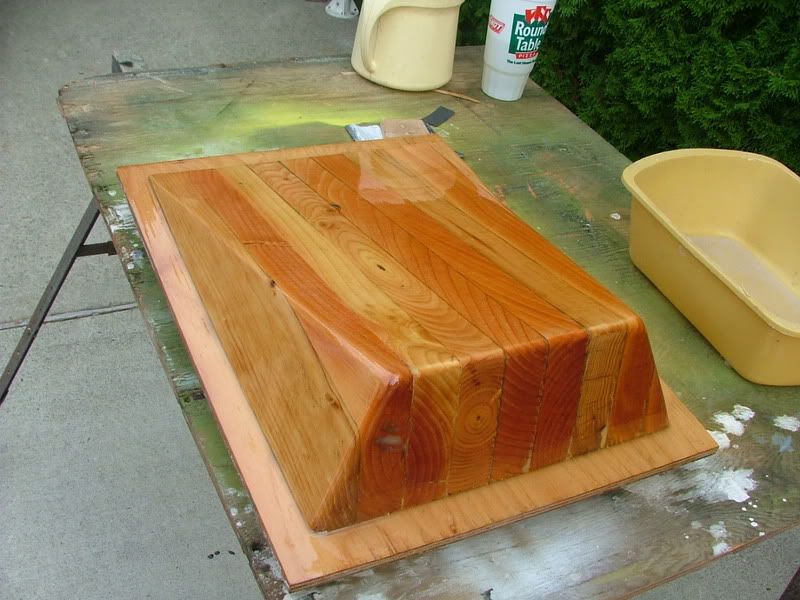
I started to lay up the glass cloth (picture has two layers) but was finding that the shape was making it difficult to wrap the glass and keep it well adhered to the previous application. You can also see on the forward wall where I had pieced remnants in to keep the thickness constant.
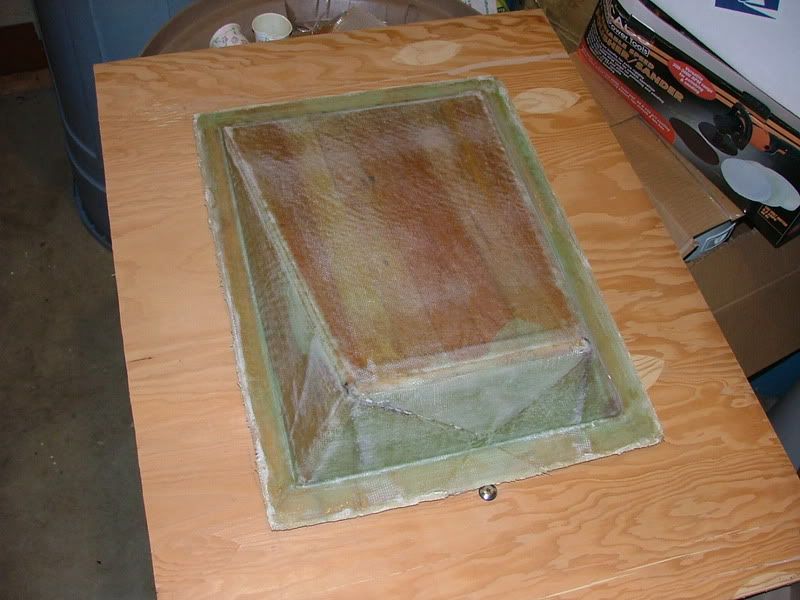
In my internet boating career I remembered seeing information about vacuum bagging and figured that would be the answer to my problem. Question was how to accomplish that without any experience and without costing an arm and a leg. I vowed that this Beachcraft project was going to be an economy project.
I now have the answer to those issues. I have obtained 66 sq yds of very slightly irregular 10oz Eglass off of ebay for about 2 bucks a yard shipped (you cannot use the dollar sign in this forum. It shows up as you type it but does not show once you post) US Composite sell the same glass for 6.70 a yard.
I also scavanged two different vacuum pumps. (an extra just in case) I have the plastic wrap material (old roll of plastic sheet from the garage) and this weekend I will attempt the process. The large board you see my part sitting on is the first step. Note the little bud coming up thru the board at the front end of the glassed part. That is my vacuum port. (a metal tire valve with rubber washers) I will post pictures as I set the rest of the process up and begin the bagging.