Re: Underskining toon ?
What I did:
I used two sheets of 4 feet by 10 feet 5052 aluminum. I choose 5052 because I understand it is more resistant to corrosion and is stiffer than the readily available 3003. I called several local shops and got a three prices from $115 a sheet to $195 a sheet, with the best price from the smallest shop.
Cost:
2 sheets .063 thickness, 5052 4 x 10 aluminum $230 plus tx.
The shop charged me $16 for 8 cuts.
100 screws at $35. They are stainless steel, with a washer, a neoprene washer and they are coated with a coating to resist seizing and corrosion. Tot 1 ? inches with about 5/8 of threads. I like the coating because I found research showing stainless steel, into aluminum, can promote corrosion especially in salt water, and a coating will help resist it.
http://www.finishing.com/271/67.shtml
I ended up with 3 sheets 57? x 48?, 1 sheet 48? x 32?, 2 side pieces 48? x 6?, and 4 side pieces 57? x 4?. I used a jig saw to cut 2" off the two 6" pieces, so all side pieces are 4" tall.
I weighed the aluminum, total 68 pounds, and the 98 screws, less than two pounds. So total weight increase 70 pounds.
I cut a 2? x 2? stringer to fit between the toons and used a couple blocks to hold the sheets in place while I used the drill to put the screws in place. I have not decided about under skinning the final two front feet.
Before putting the side pieces up, I have decided to have a 1 inch 75 degree bend put in them, so the ? gap at each side will be covered up. I have watched the water under the boat at speed, and the water hits in the center, but then is deflected to the sides, so I want the gap filled.
I took 4 hours, by myself, taking my time, with a 30 minute break along the way. Nursing a bad back and knee surgery 3 months ago.
I know you guys like pictures, so here you go.
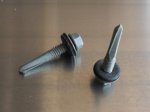
Screws, 1 1/4", coated, stainless, washer and neoprene washer
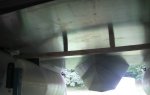
First sheet being held in place by a board and couple pieces of 2x4
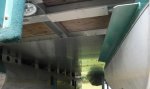
All four underskin pieces up. I'm not doing the first two feet at this time.
-------------------------------------------------------------------------------------------------------
Installing the side pieces.
The original skin was 57? x 48?. That 57? left a gap of ? to ? inch at each side.
The side pieces measure 57? x 4?. I decided to get a one inch bend of 75 degree on the side pieces to cover up that gap, and make the side pieces stronger. I choose 75 degrees instead of 90 degrees so the side piece would snug up to the top better, and any pressure would snug it up more. The shop charged me their minimum shop time, $16, to make the bends. If I had thought ahead, I think that would have been included in the origional purchase, because it only took them 5 minutes.
I left the ? gap at the bottom for quick, easy draining.
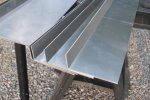
The 75 degree bend.
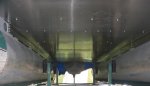
Finished for now